Types of Warehouse Pallet Racking & Shelving
Planning your shelving and racking is very important for your business. When searching for a pallet rack system, it’s easy to forget that one size doesn’t fit all. This also applies to warehouse shelving storage. There are many variables to consider when choosing your pallet rack and shelving, such as your space, inventory, and more.
Within this article, we will go over these common types of warehouse racking and shelving:
- Shelving
- Racking
Differences Between Shelving and Racking
Shelving is for hand-stacked storage: items in boxes or bins or loosely stored by someone hand-loading onto shelves.
Pallet rack is primarily for palatalized storage: inventory on pallets that are loaded and unloaded with a forklift. The lower levels of selective pallet rack can also be used for hand-stacked storage as well.
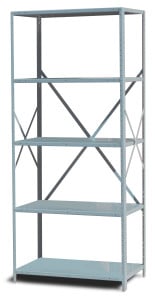
Many warehouses use pallet racking because it creates a convenient shelf for pallets and inventory.
Types of Warehouse Storage Shelves
Metal industrial shelving
Use metal industrial shelving to organize smaller hand-loaded inventory. Industrial shelving is a versatile storage system that accepts materials in a variety of shapes and sizes. Open shelving allows for visibility, making it easy to hand-pick inventory. Closed shelving is ideal for items that can’t be contaminated by dust or light.
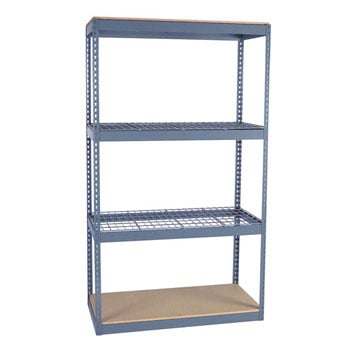
Boltless rivet shelving
Boltless shelving is the ideal heavy-duty solution. It is easy to assemble and reconfigure without hardware, nuts or bolts. These racks are durable and versatile, making them good for any warehouse.
Bin shelving
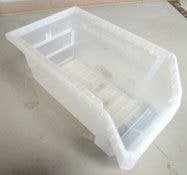
Storage bin shelving contains plastic bins on its shelves or has dividers built into the system. Storage bins can be used as a place holding device to keep like-items in one area or to prevent items from falling through your racks. You can add a letter or number system to the bins for better organization. Storage bins are useful for smaller amounts of items, rather than large pallets.
Mobile aisle shelving
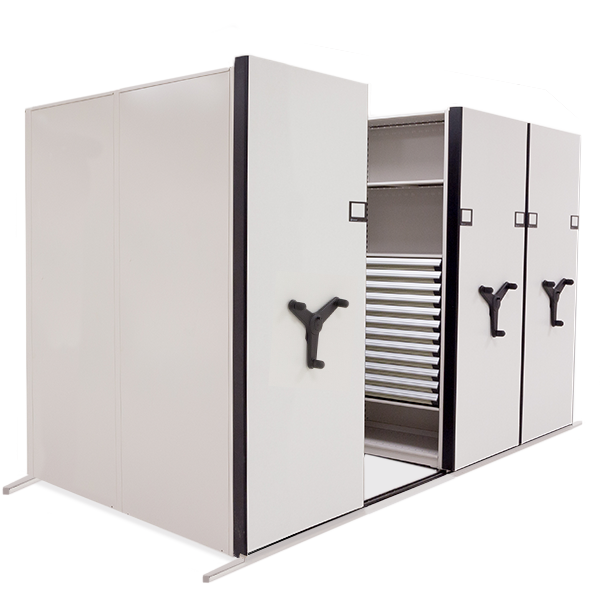
Mobile storage shelving usually has a rotary handle on the side of the shelves, and when they are rotated, it winds the single, connected filing unit either left or right depending on the rotation. These types of shelves are great for offices with limited space.
Pallet Racking Types
Selective pallet rack
Selective rack is the most common pallet racking system. These styles make the pallets accessible from the aisle with multiple beams in place for support. Usually these are associated with narrow aisles but there are both standard and deeper reach options. The deep reach variation provides double the storage space and should be a consideration for those with large storage needs but more limited space for the racking.
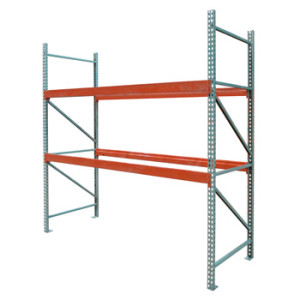
With a selective rack, you can use either a first in first out (FIFO) or last in first out (LIFO) system, freeing up shelf space as you need it. However, be aware of your ceiling heights. Too many pallets in one bay can cause a dangerous situation, while too few won’t utilize your space properly. Selective racking is best if you want to use both FIFO and LIFO loading systems and if you need accessibility to all pallets at one time.
Push back racking
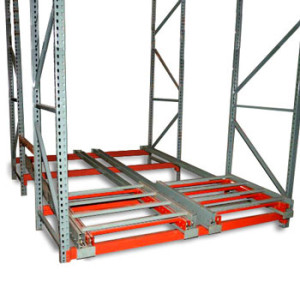
Push back eliminates any need for aisles, reducing the risk of damage. This storage option provides last-in-first-out product management and is great for alike products stored in bulk.
To load, lift drivers will set pallets in the front of the system on a rail cart. As more pallets are added to the rack, the last pallet is pushed one position farther into the rack. A gravity system makes unloading an easy task with gravity feeders that push the next pallet in line toward the unloading space. This solution is perfect for warehouses that store different product types in one area.
Flow rack systems

Flow rack systems allow the inventory to flow out of the bay with minimum labor. They use gravity roller conveyors with slightly pitched wheels to transport inventory. Once the pallet is unloaded, the next one slides into the slot. Flow racks can be 20 or more pallets deep and there’s no potential damage from driving into the bay. These racks, however, are the most expensive options and they do not give you access to all the pallets at once.
Drive-in racks

Drive-in racks are often used for high-density storage. They’re called “drive-in” because they’re designed in a way that allows the forklift to drive directly into the bay to deposit and remove items. These racks have one entry way and one exit, where the similar drive through rack provides entry and exit from both sides.
Drive-in racks utilize a last-in-first-out system, making them great for long-term storage but not recommended for items that could perish, since many items might be pushed toward the back of the structure for long periods of time.
Choosing the Best Option
When choosing your racking and shelving, think about all options and which will work best for your warehouse's setup and needs. Remember to look at the layout of your space and be sure to think about proper organization for all your inventory and tools.
For any questions about your racking and shelving, contact Warehouse1 or call 816-483-6999.